Conducting Periodic Inventory Count
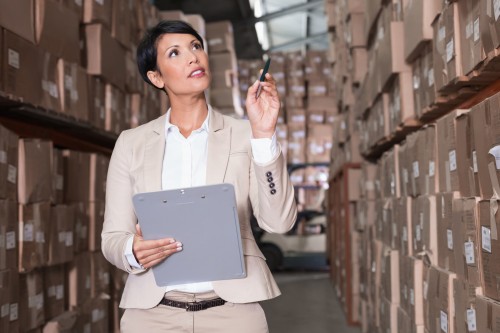
One of the most challenging tasks in accounting for retail or manufacturing business is the conduct of periodic inventory count. This is especially true for those who are assigned to do this task but don’t have the hands-on experience. The questions that come into mind includes on how to conduct the count and ensure that the activities are properly carried out. This article aims to give you an idea of how to get ready for a periodic physical inventory count and the steps involved to have a successful inventory count.
There are types of business that require more focus and attention to physical inventories, especially those engaged in trading or buy and sell, those that store inventories in bulk, be it raw materials, in process goods as well as office supplies, store supplies and other inventory items. The following are some of the steps involved in conducting physical inventory count:
1) Always have the pro-forma Count Sheet ready and properly planned so that the warehouse or inventory custodian use this form. A column for the custodian’s count and another column for the actual count should always be included in this form as well as portion for the custodian’s signature especially in case of count discrepancies.
2) Reach an agreement with related departments on when the count is to be conducted and the start time and expected time to finish the inventory count. Proper planning of the day or days the count is to be conducted will not hamper operational and store operations if the establishment company is on the retail side, like the case of stores located in commercial malls.
3) Agree on the cut-off date and time for which transactions need to be entered for count purposes. For example, you will be conducting count of office supplies at the main supplies room, you have to designate the date and time to receive supplies requisition.
4) Coordinate with the inventory or warehouse custodian to ensure that the items to be counted are systematically organized and sorted for the count purposes. For example, the supplies are in boxes containing 50 units each, these should be indicated in their count sheet and the loose quantities indicated too.
5) During the count, safety and security measures shall be observed whenever possible. For example, for store locations, the finance or audit personnel verifying the count should place their personal belongings on the designated secure lockers. While this may be considered as excessive measure, the advantages of this usually pay off for the mutual benefit of the parties involved in the count.
6) Any count discrepancies should always be noted by the warehouse or inventory custodian. It could be there is no discrepancy between the count and further count on the unreconciled items counted will prove some count mistake. Otherwise, if there is a discrepancy, it should be signed noted by the responsible custodian.
7) To ensure that all areas and items are counted, the duplicate count sheet should be placed on the items being counted to avoid mix-up of counts. The printed name and signature of the one verifying the count should be indicated in the Count Sheet form.
8) Sign-off by the count verification team should be properly noted by the warehouse or inventory custodian as well as the security team.
9) All inventory counts results should be immediately posted to the accounting or inventory system and official count results released to the involved parties.
10) Most often, conducting the count can also be a reliable avenue to introduce process improvements on how the items are kept in the storage area as well as the surroundings of the items location to identify possible and probable risks that may involve the safety of the stored items as well as the people involved.
The above are just some of the general steps involved in the conduct of the count and will apply according to the company’s type of business.